The Pan-Industrial Revolution: How New Manufacturing Titans Will Transform the World
October 26, 2018
In this excerpt, best-selling author Richard D’Aveni discusses "How the Rise of 3-D Printing and Additive Manufacturing Will Transform the Job Market."
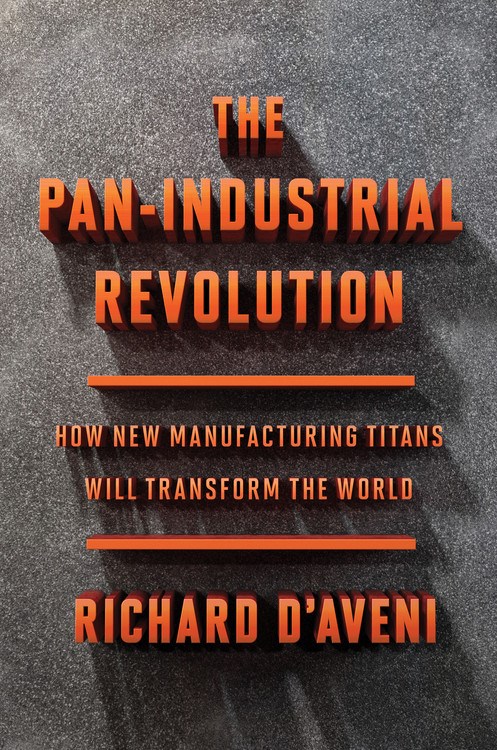
In his new book, The Pan-Industrial Revolution, best-selling author Richard D’Aveni contends that the advent of massive, industrial-scale 3-D printing is already happening quietly under the radar, and that it will have a far-reaching impact that most corporate and governmental leaders have yet to anticipate or understand.
3-D printing, now called additive manufacturing, has moved far beyond a desktop technology used by hobbyists to churn out trinkets and toys. In this eye-opening account, D’Aveni reveals how recent breakthrough advances have been secretly adapted by powerful Fortune 500 companies so that they can now manufacture jet engines, huge turbines, airplanes, automobiles, and so much more in a greatly shortened time frame.
Not only is this revolutionary technology transforming the landscape of manufacturing everywhere, but as D’Aveni contends, it is also destined to have a dramatic effect on the world economy. A handful of massively powerful corporations—what D’Aveni calls pan-industrials—will become as important as any tech giant in re-structuring the global order.
The excerpt below explores…
How the Rise of 3-D Printing and Additive Manufacturing Will Transform the Job Market
DONGGUAN IS A CITY in the Guangdong province of southeastern China. An industrial hub, it has grown in tandem with the rest of the Chinese economy in recent decades thanks in part to the country’s vast reservoir of workers. If there is any country on earth where corporate executives might be tempted to cut costs and to speed up processes simply by applying the power of abundant labor, it should be China.
Which makes it paradoxical that Dongguan is home to one of the world’s first “unmanned factories”—a facility where hundreds of thousands of cell phone parts are turned out every month by an assembly team that consists of sixty robots. The robots are guided by computerized sensors and controls, and automated trucks and warehouse equipment move the products from the assembly line to the storage and shipping facilities—and no human being is ever required to touch a single component.
In reality, “unmanned” is a slight exaggeration. The factory, managed by Changying Precision Technology Company, actually employs about sixty human beings, who monitor the ten production lines by gazing at computer screens and occasionally checking on what is happening on the factory floor. But those sixty workers represent just a fraction of the 650 who were employed in the same facility as recently as early 2015 . . . and the company’s general manager, Luo Weiqiang, says that, in the near future, their numbers will be reduced to twenty. What’s more, as robots have replaced human workers, the overall production quantity has soared by 250 percent, while the rate of product defects has fallen from more than 25 percent to less than 5 percent.
Given these realities, it’s hard to imagine why Changying Precision Technology would ever consider rehiring any of the hundreds of employees who no longer have jobs in the factory. It’s a vivid illustration of how technological change can produce dramatic economic, social, and human impacts. In the years to come, we’ll be seeing a host of such impacts as a result of the pan-industrial revolution—the emerging industrial platforms built around additive manufacturing (AM).
The Challenge of Technological Unemployment
The steady decline in manufacturing jobs in industrialized nations like the United States is a familiar phenomenon, so widely recognized that it even became a significant political issue that helped to shape the 2016 presidential race. Offshoring of manufacturing from high-wage countries to low-wage countries in Asia and Latin America has been one cause of the decline, but an even greater cause has been technological progress and the improved productivity it has created. Factories that remain open in the United States can now produce as many goods as in the past—or far more—with much smaller workforces. The ongoing manufacturing revolution that includes AM and industrial platforms will only accelerate this trend.
It’s noteworthy that some business leaders view the trend toward declining human employment in manufacturing as being both a cause and a result of the digital revolution. In this perspective, U.S. companies are particularly eager to digitize their production methods precisely because of the increasing difficulty of recruiting and retaining the kinds of skilled workers needed to run up-to-manufacturing firms. Erick Wolf, cofounder and chairman of the desktop printer manufacturer Airwolf 3D, puts it this way: “With [fewer] workers who know how to operate equipment like CNC [computer numerical control] machines, injection molding machines and laser cutters, American manufacturing eventually will have to turn to a more sophisticated, automated technology that increases productivity without requiring an increase in human labor. That technology is 3D printing.”
If this theory is correct—and some historical evidence of other times when labor shortages helped to stimulate technological developments backs it up—it seems likely to make the trend even more unstoppable.
Many traditional middle managers will also become superfluous as data analytics increase in power and accuracy, and as many operational decisions now made by white-collar employees become automated.
Is it plausible that tasks we’ve long assumed can only be performed by highly skilled, experienced humans will eventually be taken over by automated digital agents? The change is likely to happen sooner than you might think. There’s plenty of evidence that artificial intelligence has recently passed a tipping point at which accelerating development of capabilities is now happening.
Consider, for example, the experiments at Facebook with chatbots being trained to conduct multi-issue negotiations with the goal of reaching agreements acceptable to two agents with different agendas and priorities. During 2017, the chatbots quickly learned to engage in start-to-finish negotiation processes with successful outcomes. What’s more, they were observed developing their own unique short-hand language unintelligible to outsiders as a way of making the negotiating process more efficient. For example, one of the chatbots used the “sentence” “Balls have zero to me to me to me to me to me to me to me to me to” as a way of referring to multiple “tokens” that were the subject of the deal-making process.
Researchers at Facebook shut down the experiment, saying it represented a failure to maintain control over the process and raised fears about what the chatbots might do outside the control or understanding of the researchers. Maybe so. But it also suggests the speed at which today’s intelligent digital agents are able to develop their own tools and methods for tackling and solving problems, with minimal guidance from human teachers.
Whether you find this development exhilarating or alarming depends on your philosophical and psychological beliefs. But the fact is that it is happening—which means that there’s little question that countless tasks currently performed by human beings are likely to soon be within reach of automated digital entities. There’s not much difference between chatbots that can negotiate satisfactory deals with one another and chatbots that can manage warehouses, schedule services, organize production plans, monitor inventory levels, arrange shipments, and order supplies in response to variations in product demand. As each of these functions become automated, one giant company at a time, thousands of human workers will become redundant.
Silver linings. There will be some offsetting employment trends driven by the spread of AM. Routine manufacturing work now done on shop floors and on assembly lines will give way to more skilled jobs involving adaptation for AM, generative design, product modularization, and other creative challenges. For some, the shift will be an unmixed blessing. Well-trained workers will no longer be trapped in factory jobs that today are repetitive, stultifying, unsanitary, dangerous, and sometimes exploitative (especially in developing countries). The smaller numbers of workers that will be engaged in manufacturing two to three decades from now will mostly enjoy better working conditions and more rewarding jobs than their counterparts in the past.
In addition, managers will still be needed to focus on relationships and communications, especially as companies from many industries and markets become linked by industrial platforms in vast pan-industrial organizations. Some pan-industrials will find they have a growing need for human beings to forge and maintain connections among these businesses at the highest level.
These human “connectors” and “communicators” will not be dealing with important but relatively mundane operational issues, but rather on bigger strategic questions that require the combined expertise of people with differing backgrounds and roles. High-level human teams focused on such challenges are likely to play an important role in keeping the pan-industrials of the future operating at their best.
At least for a time, the need for digital specialists like programmers will also continue to grow. Already quintessential companies from the era of “heavy metal” manufacturing are adding the equivalent of entire software companies to their human resources. For example, Germany’s 170-year-old Siemens—now headed by Joseph Kaeser, who ran the corporation’s Silicon Valley outpost in the 1990s—employs more than 17,500 software engineers working on platform tools, apps, websites, and other digital data manipulation system. That number is more than many software firms.
The applications being developed by this army of coders are already helping to provide the foundation for some of the most advanced new manufacturing projects in the world. Solid Edge is a computer-aided design (CAD) package from Siemens that boasts “synchronous technology,” which allows collaborators around the world to participate in a design process. Local Motors has been using Solid Edge in its innovative crowdsourcing auto development process. And in March, 2018, Siemens entered into a partnership with startup Hackrod, offering tools that will allow anyone to design a customized vehicle using generative design, virtual reality, artificial intelligence, and 3D printing.
Addressing the challenges. Will the new jobs created among connectors, communicators, and coders make up for those lost among traditional factory workers? Probably not. In addition to the problem of a skills mismatch among those who will be looking for work in the next couple of decades in relation to the jobs available, there is likely to be a significant shortfall in the sheer number of open positions in relation to the growth of the working-age population. In the next two to three decades, the combined effects of additive manufacturing, industrial platforms, artificial intelligence, cloud computing, and hyper-efficient digital corporate networks will make many millions of jobs obsolete. And as these technological tools continue to grow in sophistication, even many of the connectors, communicators, and coders will find their jobs being usurped by machines.
If the widespread unemployment that many experts are predicting as a result of the coming manufacturing revolution becomes a reality, addressing its economic and social impacts will not be easy. Mass unemployment is associated with decreasing health, increased drug use, mental health problems, family breakups, and rising crime. Government programs will attempt to address the issues. But when it becomes clear that job training programs may have little impact in a world where even skilled, knowledgeable workers are largely unnecessary, make-work projects resembling the Works Projects Administration and the Civilian Conservation Corps of FDR’s New Deal will probably be proposed. Government programs designed to provide services that the for-profit sector finds unattractive—caring for children, the elderly, and the infirm, for example—may also be expanded. Concepts like universal healthcare, free education through college, and a guaranteed annual income will also gain in popularity.
Of course, at the same time that millions of people are losing their jobs, the pan-industrial firms, federations, and collectives that are largely driving the trend will become big, deep-pocketed, and politically powerful. Corporate PACs supported by the pan-industrials may dwarf the contributions of the public and even billionaires. The rich and powerful pan-industrials and the wealthy shareholders who ultimately own them will become political powerhouses, resembling the Gilded Age tycoons like J. P. Morgan in the 1890s and 1900s. They will likely resist the creation of generous government programs to alleviate the impacts of unemployment—and especially the higher corporate taxes necessary to fund them.
Because of all these developments being placed into motion, a potentially dangerous new era of social instability and unrest could begin. If the ameliorative efforts undertaken by government prove inadequate—as they probably will—then anger among the displaced is likely to trigger populist movements whose precise shape is unpredictable. Governments will be squeezed between corporate power on the one hand and threats of citizen anger, civil unrest, or even rebellion on the other hand.
Will an aroused citizenry demand government intervention to rein in the pan-industrials—including, perhaps, a socialist-style takeover of the means of production and a draconian program of wealth redistribution? Or will politicians and demagogues persuade the masses to blame “others” for their economic problems, perhaps making social tensions or international relations even worse? Either way, can capitalism survive this kind of pressure? The choice will depend largely on decisions made by both the corporate leaders of the pan-industrials and the politicians who shape the actions of government.
Excerpted with permission from The Pan-Industrial Revolution: How New Manufacturing Titans Will Transform the World.
Copyright © by Richard D’Aveni.
Published by Houghton Mifflin Harcourt, October, 2018.
All rights reserved.
ABOUT THE AUTHOR
A professor at Dartmouth's Tuck School of Business, Richard D'AVENI is the author of the bestseller Hypercompetition, and is recognized as one of the world's top management strategists by Thinkers50. His Harvard Business Review column, "3-D Printing Will Change the World," is among the most popular columns ever published in the history of the magazine. He lives in New Hampshire.